Volkswagen Gigafactories in Europe “We are ensuring that our e-offensive gets up and running”
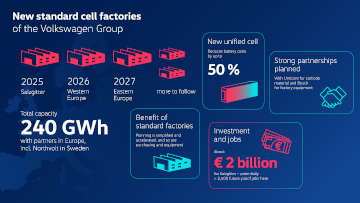
In order to meet the increasing demand for electric cars, the Volkswagen Group is planning to build several gigafactories. The battery cells produced will be used in models in the ID. family, among other things. As Head of Operations Battery Cell Volkswagen Group, Sebastian Wolf is responsible for the construction of the factories. In an interview, he presents the plan.
You plan to build five cell factories in Europe by 2030. How much respect do you have for the job?
I don’t want to talk it down: constructing the gigafactories is a major project, which will really ask a great deal of us. We are now building multiple cell factories. It comes down to three things. Firstly, a strong team – that is why we have added more top experts from the international battery industry and will continue to expand the team. Secondly, the right partners – for the construction of the buildings and production plants. Thirdly, standardisation. If we plan each plant individually, it will take too long. That is why we have gone for the concept of a standard factory, whilst at the same time remaining adaptive and flexible. This way, all the locations will go operational on time.
What are the benefits of a standard factory?
The standard design simplifies and, above all, accelerates planning and purchasing, as we can use the same components for the buildings and equipment in all the factories. Only the approval procedures in the various countries are different. The basis for the standard factory is the Volkswagen unified cell, which we are manufacturing at all locations. The combination of the two leads to high economies of scale. From a customer’s point of view, this will have a positive effect on the price of the vehicle.
Together with Bosch, Volkswagen is looking into founding a European supplier for battery cell factories. What role does this play in your plans?
Far from a small one. Over the next few years, quite a few major battery production projects will be launched in Europe. We see great potential in getting involved together in the factory equipment stage of the value chain. Both parties have innovation competence and are capable of globally networked, mass industrial production. Among other things, Bosch develops tailor-made machines and facilities, and delivers digitally controlled assembly lines.
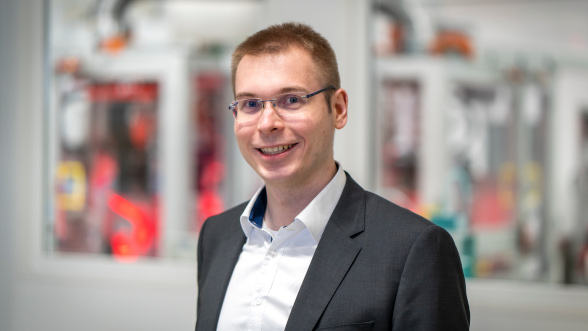
Sebastian Wolf
You also have plans to collaborate with the Belgian battery materials specialist Umicore. What will that involve?
We want to set up localised added value with this project as well, to counteract potential bottlenecks. We’re talking to Umicore about setting up extensive production capacities for cathode materials. We are also discussing the procurement of raw materials and recycling.
How much is going to be invested in the cell factories overall?
The Group is investing around 2 billion euros in setting up and running the cell factory in Salzgitter. We are not the sole investors in setting up the entire value-added chain in Europe, we also have strong partners involved. Which is why Volkswagen is founding a European corporation to bring all the activities under one organisation – from the processing of raw materials, through the development of the unified cell, to managing the gigafactories.
The cell factory in Salzgitter is set in stone, Spain and Eastern Europe are under discussion, and additional locations are being investigated. According to which criteria will you make your selection?
As well as procuring the land and local contexts, two things are decisive: personnel and energy. In order to get a cell factory up and running, we must find enough qualified employees in the surrounding area. Not only chemists, that is a manageable number, but above all people with production experience. We also need sufficient green electricity, such as from solar power and wind farms.
How adaptable are the factories, should battery technology continue to develop?
The planning of the standard factory is based on our technology matrix, which covers more than 30 foreseeable process innovations by the end of the decade. They include the dry coating of electrodes, new cellular chemistry, and solid-state batteries. We are assuming that we will continue production throughout three factory generations. A number of process chains will change, and we will replace some facilities. Each generation of standard factory is designed in such a way that we are always upwardly compatible and thus ensure that we can use the investments in the long-term.
Volkswagen partner Northvolt is building another factory in Skellefteå in northern Sweden. In what way does this factory differ?
Northvolt will not only supply brands within the Volkswagen Group, but also other customers. Accordingly, we will not only produce unified cells in Sweden in the future, but also other cell formats. Regardless of that, cell production in Skellefteå is designed to use renewable hydropower.
How many jobs will the six factories generate?
We are talking about a five-figure number of jobs in total. In Salzgitter alone, more than 2,500 workplaces will be created.
You touched on the subject of finding personnel. Where will the workforce come from?
Salzgitter is the first location, for which we have begun concrete planning. I am assuming that we will find the majority of employees within the company. That is part of the transformation at Volkswagen. For example, there are many production professionals at the engine plant in Salzgitter, who could work in the new cell factory after attaining the necessary qualifications. The product may be different, but many of the manufacturing processes do not differ so greatly.
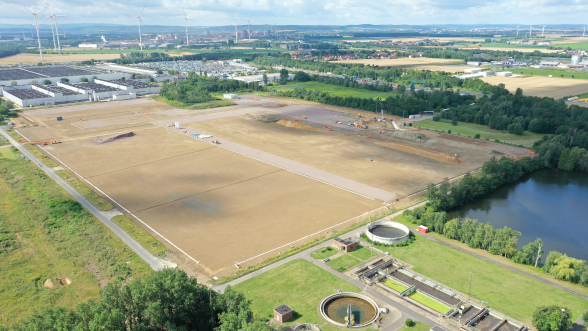
What does the time plan look like?
In Salzgitter, the levelling – the preparation of the plot – is almost completed. In March, we will submit the planning application and potentially start construction in the second half of the year. The first factory block should commence mass production in spring 2025. After roughly half a year, the second block will start. This will be followed, in intervals of a few months, by the other locations, starting in southern Europe. We plan to achieve a total capacity of 240 GWh by 2030 at the latest.
Does this make Volkswagen self-sufficient, or must you still purchase cells?
Through in-house manufacturing, we are ensuring that our e-offensive gets up and running and moving towards greater independence. We will also continue to use purchased cells. It obviously depends a little on the customers: the faster electromobility comes to the fore, the faster the demand for battery cells will grow.
So far, Asian manufacturers have been seen as the leaders. Do cell factories also have significance regarding industrial policy?
With an e-car, the battery cell is a central distinguishing feature. It is key to charging speed and range. As such, I believe it is hugely important to increase know-how in Europe and to bring value chains to us. Similar to how it is today with the combustion engine. In the case of battery cells, we are nothing more than fast followers at the moment, but if we do things right, we can be among the leaders in a number of years.
About the person:
Sebastian Wolf has been Head of Operations Battery Cell in the Battery division since August 2021. As such, the production engineer is responsible for construction of the European cell factories, which will supply energy storage devices for the Volkswagen ID. models. Before joining the Volkswagen Group, Wolf worked for Chinese battery manufacturer Farasis Energy, most recently as Managing Director Europe. After passing his school leaving examinations in Istanbul, Wolf studied at universities in Aachen, Bath and Tsinghua in Beijing. As well as German and English, he also speaks Chinese, French and Turkish.
European company
The Societas Europaea (SE) or European company allows business operations in various European countries, in accordance with a standard set of regulations. In Germany, this business form was introduced in 2004. The SE founded by Volkswagen for battery business bundles the activities along the value chain – from the processing of raw materials and Volkswagen’s development of unified cells to the control of European gigafactories. The SE will also be responsible for new business models, such as the recycling of raw materials.