Per la prima volta un gruppo di ricerca guidato dal Gruppo Volkswagen lavorerà sul riciclo multiplo delle batterie
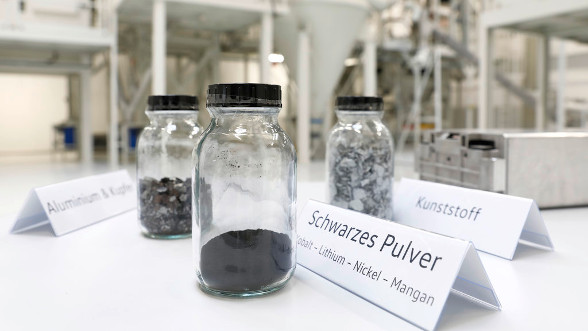
I partner della comunità industriale e scientifica intendono dimostrare che i componenti più preziosi delle batterie da trazione possono essere recuperati e riutilizzati più volte consecutivamente mediante il loro riciclo. Il consorzio di ricerca HVBatCycle ha l'obiettivo di mantenere in un ciclo chiuso i metalli del catodo, l'elettrolita e la grafite in modo continuo. Guidati dal Gruppo Volkswagen, TANIOBIS GmbH, J. Schmalz GmbH e Viscom AG collaboreranno per tre anni con i ricercatori dell'Università Tecnica (RWTH) di Aquisgrana, dell’Università Tecnica di Braunschweig e dell'Istituto Fraunhofer per l’Ingegneria delle Superfici e dei Film sottili (Fraunhofer Institute for Surface Engineering and Thin Films, IST) per studiare e lo sviluppare i processi necessari. Il progetto è finanziato dal Ministero Federale dell'Economia e dell'Energia.
Michael Kellner, Segretario di Stato parlamentare: “La produzione europea di batterie può avere successo solo se si concentra sulla sostenibilità considerando più aspetti possibile. Le batterie sostenibili sono fondamentali per una transizione energetica e dei trasporti guidata da elevati standard ambientali e sociali”.
Sebastian Wolf, Responsabile delle operazioni Battery Cell del Gruppo Volkswagen, ha spiegato: "Il riciclo delle batterie e degli scarti di produzione contribuisce in modo decisivo a garantire l'approvvigionamento di materie prime per le nostre fabbriche future. Con il progetto HVBatCycle si lavorerà a una visione olistica dei processi di riciclo, e quindi all'implementazione del ciclo chiuso dei materiali per le batterie".
Ciclo chiuso delle materie prime e riciclo multiplo
Per utilizzare meno materiali provenienti da fonti primarie come miniere o saline, le materie prime essenziali devono essere recuperate non una, ma più volte. A tal fine, le celle batteria già realizzate con materiale riciclato vengono nuovamente riciclate, dimostrando come ciò non vada a intaccare la qualità del materiale. Chiudere il ciclo richiede complessi processi interdisciplinari. Questi devono essere coordinati tra loro per produrre materiali secondari selezionati e di alta qualità, nel rispetto dei massimi requisiti di sicurezza; ciò è fondamentale anche perché il riciclo sia efficiente e sensato dal punto di vista non solo ecologico, ma anche del business - questioni di scalabilità ed efficienza economica, in particolare.
Indipendenza grazie alla decentralizzazione, vantaggi legati all'impiego di materiali secondari
Il progetto del consorzio si concentra sul percorso di riciclo meccanico-idrometallurgico, caratterizzato da un basso fabbisogno energetico e dalla possibilità di una distribuzione decentralizzata relativamente semplice di alcuni processi in Europa. Ciò favorisce un'economia circolare locale e assicura materie prime strategicamente importanti, riducendo in modo significativo la dipendenza dell'Europa da altre regioni del mondo. Il progetto HVBatCycle mira a individuare processi efficienti e soluzioni innovative che garantiscano la creazione di una catena del valore end-to-end con un'elevata efficienza economica e che, allo stesso tempo, massimizzino il riciclo e l'efficienza energetica e riducano al minimo l'impatto ambientale.
Automazione dei processi di smontaggio e recupero del materiale dell’elettrodo
Gli approcci innovativi e concreti allo sviluppo consistono in processi orientati alla domanda ed economicamente ottimizzati e nello smontaggio ampiamente automatizzato delle batterie a fine vita, fino al livello della cella o dell’elettrodo. Ciò include anche la separazione del materiale attivo e dei film di supporto quasi senza perdite, nonché il recupero della grafite e dei componenti altamente volatili dell'elettrolita.
Nel successivo trattamento idrometallurgico della "polvere nera" - costituita da grafite e metalli della batteria - per cui si utilizzano acqua e solventi chimici, l'attenzione è rivolta all'estrazione precoce e selettiva del litio in forma solubile nonché alla lisciviazione, alla precipitazione e alla raffinazione dei metalli contenuti come concentrato di idrossido misto. A questo punto, in relazione alla rinnovata sintesi di materiale attivo catodico, si studierà se la separazione dei composti metallici sia davvero necessaria per produrre nuovo materiale catodico ad alte prestazioni.
Il lavoro di ricerca sulla lavorazione dell'elettrolita e della grafite è volto a dimostrare, attraverso lo sviluppo di processi adeguati, che anche importanti componenti dell'elettrolita e la grafite possono essere lavorati in modo efficiente e riutilizzati, con una qualità adatta alle batterie, nella produzione di celle. Tutte le fasi del processo sono accompagnate da un'analisi ecologica ed economica del ciclo di vita.
Informazioni sui partner del progetto:
Nell’ambito delle proprie strategie per le batterie e la sostenibilità, il Gruppo Volkswagen guarda con molto interesse alla realizzazione di un ciclo chiuso dei materiali per le celle e ha quindi assunto il coordinamento e la gestione del progetto. Grazie all’impianto pilota per il riciclo meccanico presso il sito di componentistica di Salzgitter, la Divisione Tecnologia del Gruppo è in grado di produrre e fornire materiale riciclabile dalle batterie dei veicoli. Inoltre, l’esperienza nella produzione di celle presso il Centro di Eccellenza di Salzgitter sarà utilizzata per produrre nuove celle da materiale completamente riciclato.
TANIOBIS GmbH è un affermato fornitore di polveri contenenti niobio e tantalio per i processi produttivi idrometallurgici, inclusa l'estrazione con solventi. In quanto filiale di JX Nippon Mining & Metals, possiede una conoscenza approfondita del processo idrometallurgico per il riciclo delle batterie agli ioni di litio, che sarà utilizzato nel progetto. Sulla base di ciò, TANIOBIS GmbH costruirà e gestirà l’infrastruttura idrometallurgica e pirometallurgica necessaria presso il polo chimico di Oker, dove è presente anche un laboratorio di analisi certificato.
J. Schmalz GmbH è azienda leader nel campo della tecnologia del vuoto, e uno dei pochi fornitori di soluzioni complete in questo ambito. Nel segmento di business relativo all’automazione con il vuoto, Schmalz fornisce tutti i componenti necessari per assemblare le pinze di presa dei robot industriali. Inoltre, la tecnologia dei sensori di Schmalz garantisce l'efficienza e la sicurezza dei processi. In progetti congiunti con istituti scientifici, sono stati realizzati sistemi di movimentazione per wafer di silicio e lamine catodiche e anodiche.
Viscom AG sviluppa soluzioni di ispezione a raggi X specifiche per l’industria delle celle batteria. La gamma dei prodotti spazia dai sistemi di laboratorio a soluzioni complete in linea per un controllo qualità al 100% ad alta velocità. Viscom è specializzata in diversi formati di celle, come le celle pouch (a sacchetto) o quelle prismatiche, che coprono diverse dimensioni per prodotti di consumo, sistemi di accumulo energetico e batterie per la mobilità elettrica.
Il Battery LabFactory Braunschweig (BLB), centro interdisciplinare dell’Università Tecnica di Braunschweig, è una delle istituzioni leader nel campo della ricerca sulle batterie in Germania. Il BLB è una piattaforma R&D per la produzione circolare, la diagnostica e la modellazione/simulazione di batterie della generazione attuale e di quelle future. Nel proprio impianto pilota, il BLB raggruppa il know-how dei processi ingegneristici, le competenze sulla scienza dei materiali, la conoscenza scientifica dei sistemi di celle per batterie dalle scienze naturali e solide capacità analitiche.
L'Istituto per le Macchine Utensili e la Tecnologia di Produzione (Institute of Machine Tools and Production Technology, IWF) si concentra sulle questioni tecnologiche e di automazione lungo le catene di produzione, attuali e future, delle celle per batterie.
L'Istituto elenia per la Tecnologia ad Alta Tensione e i Sistemi Energetici (elenia Institute for High Voltage Technology and Power Systems) ha una vasta esperienza nel campo della formazione, dell’invecchiamento ciclico e della caratterizzazione elettrica ed elettrochimica delle celle batteria.
All’Istituto per la Tecnologia delle Particelle (Institute for Particle Technology, iPAT) si studiano i processi meccanici e di tecnologia delle particelle per la produzione di materiali ed elettrodi per batterie, nonché i processi meccanici e termici per il riciclo delle batterie.
L’Istituto di Ingegneria Chimica e dei Processi Termici (Institute of Chemical and Thermal Process Engineering, ICTV) vanta un’ampia esperienza nella separazione di miscele di fluidi.
L’Istituto di Ingegneria dei Sistemi Energetici e di Processo (Institute of Energy and Process Systems Engineering, InES) ha molti anni di esperienza nella modellazione e nella simulazione delle batterie, nell’analisi elettrochimica e nell’analisi operativa.
L'Istituto Fraunhofer per l’Ingegneria delle Superfici e dei Film sottili (Fraunhofer Institute for Surface Engineering and Thin Films, IST) svolge un’intensa attività di ricerca e sviluppo in diverse aree: sintesi e funzionalizzazione dei materiali, trattamento e modifica delle superfici, produzione e applicazione di pellicole, la loro caratterizzazione e analisi delle superfici e tecnologia di produzione. Argomento centrale per il Centro progetti Fraunhofer per l’Accumulo di Energia e Sistemi di Gestione (Fraunhofer Project Center for Energy Storage and Management Systems, ZESS), la ricerca sulle batterie si concentra sullo sviluppo dei materiali e dei sistemi di accumulo dell’energia, incluse le relative tecnologie di processo e di produzione, e la progettazione olistica e sostenibile del ciclo di vita.
L’Istituto per l’Ingegneria dei Processi Metallurgici e il Riciclo dei Metalli (Institute of Metallurgical Process Engineering and Metal Recycling, IME) dell'Università Tecnica (RWTH) di Aquisgrana vanta molti anni di esperienza nella ricerca applicata sui processi di riciclo delle batterie. In questo caso il focus è sul recupero dei metalli preziosi contenuti nelle batterie, mediante processi termici e idrometallurgici. L’Istituto dispone di un’infrastruttura completa per testare diverse modalità di riciclo, incluso anche un innovativo forno pirolitico della Otto Junker GmbH che consente la lavorazione di quantità maggiori o di interi moduli di batterie. Grazie al proprio laboratorio interno certificato, l’IME ha accesso a molti importanti metodi analitici, fondamentali per lo studio dei possibili processi di riciclo delle batterie.